Esteve
1600 dps guarantees exact precision during operation
The pharmaceutical group, Esteve, has reorganized the internal logistics in their pharmaceutical product factory, located in Martorelles, twenty kilometers north of Barcelona. The goal in doing so was to increase storage capacity, as well as the productivity of the processes related with supplying and distributing products.
Project developed for Esteve
The order preparation system is a crucial feature, which always guarantees the necessary precision and speed in services to satisfy client requirements. At Esteve, picking fractions is carried out through a system developed by the company Pick to Light Systems, which has five stations, a checking area and another for packaging and documenting. The process ends with a variety of final consolidation channels and two labelers. Internal software manages movements inside the silo, in addition to receiving and preparing orders. In addition, it maintains an established temperature and humidity (15/25º).
Javier Traver, Logistics Manager explains that the Esteve internal logistics system manages a total of 556 pharmaceutical product references for humans and animals, and it was exactly this variety of products and the enormous volume handled that caused the switch to the system designed by the Pick to Light Systems; a technology that has been proven at the highest levels.
Pick to Light Systems implemented the new logistics system in approximately four years, including the phases of consultation, design and implementation, a period that was guaranteed for logistical operation of processing fractions.
“When we chose Pick to Light (PTLS), Esteve considered other proposals that were discarded in favor of the L-Pick from Pick to Light Systems, for their accredited and proven operation and their identification system, which differentiates itself from other suppliers, by using inset pilot lights to facilitate the operator's work”, said Traver.
The Digital Picking System (DPS) from Pick to Light Systems is extraordinarily flexible and simple, which allows you to create personalized and adaptable systems to all types of operations of picking, sorting and assembling in different sectors of activity, and it is totally compatible and easy-to-integrate in any existing control and/or management system within the company.
This technology allows the operator to quickly and intuitively find out the exact location and quantity of the operation to be carried out (pick-up/delivery) through the illuminated LED's and displays, and showing the quantity in demand and forcing you to confirm each article pick-up.
In addition, interacting with the system allows the operator to carry out inventory checks, and replacement requests from the illuminated modules.
Using a system means eliminating paper use and controlling all movements electronically, which translates into an increase of productivity by avoiding having to search for lost references. By exchanging information electronically, it allows you to further monitor the work of each operator automatically.
The pharmaceutical manufacturing operations are carried out in the Esteve plant located in Martorelles, which started operating at the beginning of 1992. Its facilities are technologically equipped for more sophisticated production processes that comply with American and European standards regarding quality and safety.
The production process is highly automatized and controlled by computer, which has the double advantage of guaranteeing product quality and reducing manufacturing costs.
The plant spans a surface area of nearly 30.000 m², divided in three large production systems: solids, semi-solids and liquids. Its design responds to manufacturing needs with maximum efficiency, and features areas perfectly separated for receiving and storing raw materials, shipping finished products, the quality control labs and storing flammable materials, in addition to a pilot plant and an area for cutting edge pharmaceutical development.
Before implementing the new model, the company had an automatic storage system with a capacity of 10,000 pallets and equipped with 5 transportation elevators. The connection between the silos and shipping was carried out through a transportation network. The picking function was carried out through a bar code system, but manually, as Javier Traver explained.
The internal logistical area has experienced a deep transformation by increasing the capacity of their operations. The plant has totally automatic storage with capacity for 20,000 cargo pallets, supported by five transportation belts controlled by computer, which simultaneously inserts, stores and extracts pallets. At the same time, the order preparation system designed by Pick to Light Systems has 1,600 DPS, which guarantees exact precision during operation.
Currently, the company has regained control and execution of all processes, and can successfully face new sector requirements, such as an extraordinary increase of shipping very small fractions to pharmacies.
In addition to increasing productivity, the system has reported to Esteve a practically total reduction of the number of incidences or errors in the shipping process, and has considerably reduced the labor requirements for maintaining the system.
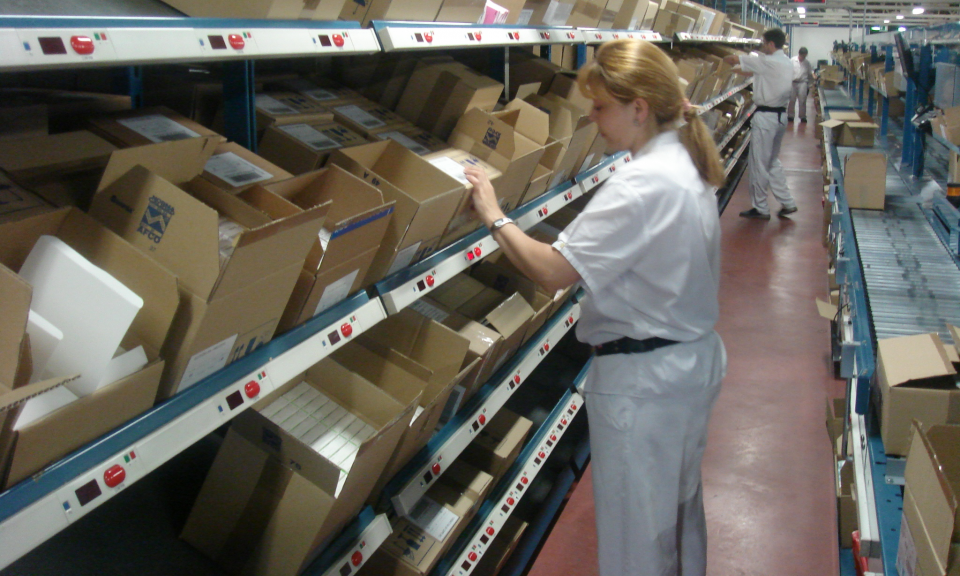
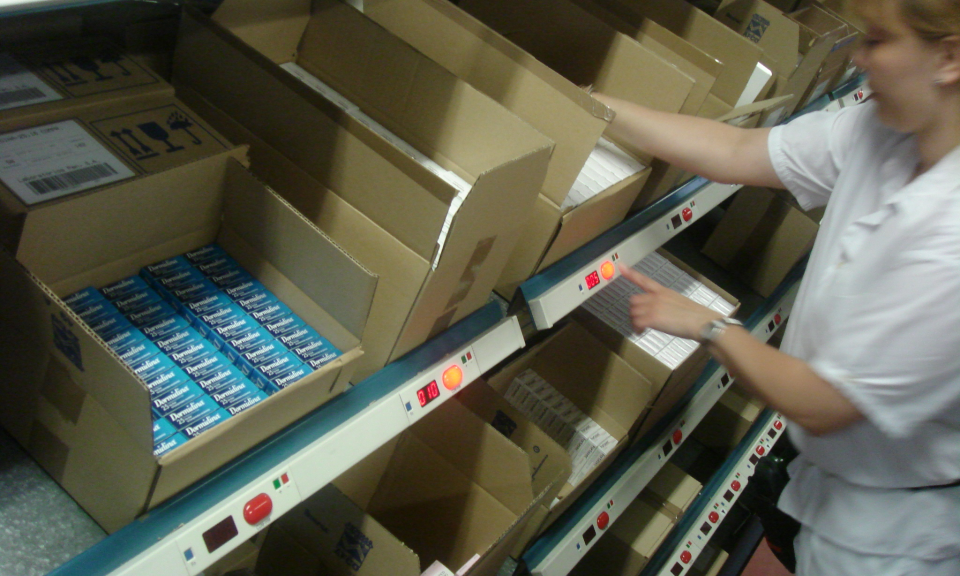