Black Friday
Can your logistics cope with the demands of ecommerce this Black Friday?
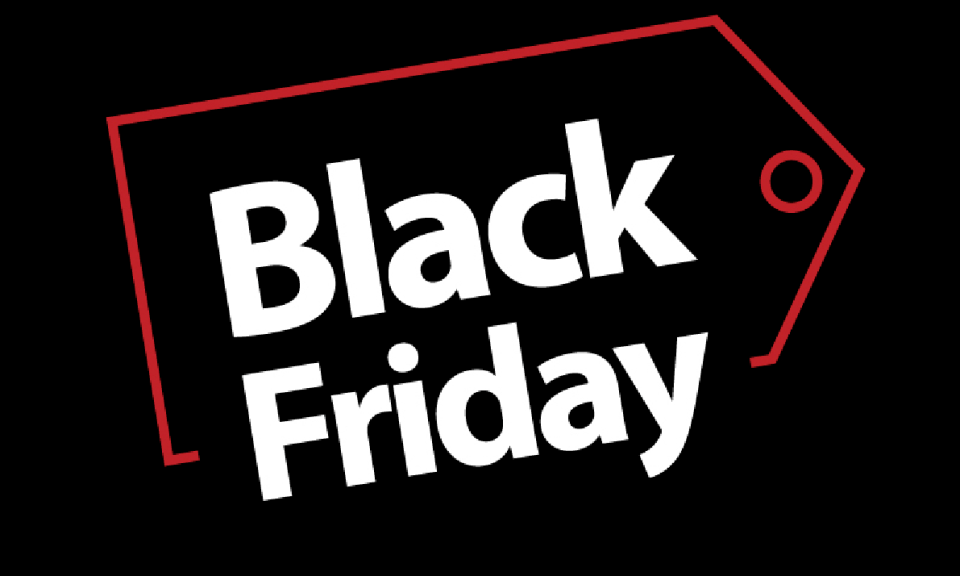
Характеристики
Introduction
With the arrival of November and just a step away from Christmas, we all look forward to one of the most important times of the year for commerce, especially for ecommerce, the famous Black Friday. One of the most important annual strategic campaigns and one that is eagerly awaited by the majority of consumers who want to do their Christmas shopping at the lowest price.
Added to the peak of sales, there is the complexity of omni-channeling: all studies predict an increase in the e-commerce channel due to the pandemic and the resulting changes in habits.
The uniqueness of Black Friday
Black Friday in 2023 will be held on 24 November, however, as we have been able to corroborate in recent years, most online retailers will not restrict their commercial strategies to this single day. Once again, we will find a long period of offers and promotions both on the eve and after the 24th. What is certain is that this will be a period of massive shopping that will have a significant impact on the logistics and distribution sector.
Therefore, companies must be prepared to cope with the huge wave of orders, both to shops and to end customers.
This important and long-awaited event has different characteristics that result in the need for sophisticated logistics to satisfy the wishes of all shoppers.
Large order peaks:
The demand for products multiplies, and consequently, the number of orders to be prepared. This makes order management in warehouses more complicated. Some of the most frequent problems are delays in the order picking due to manpower, inefficient operations that double or triple the number of warehouse staff and the need for training weeks before the start of the campaign, among others.
0 errors:
The probability of errors increases the more orders there are to prepare in the warehouse, leading to dissatisfied customers, which can damage the good work done by the company and have repercussions on online orders. It is therefore important to optimise logistics so that no mistakes are made and households avoid unpleasant surprises.
Reverse logistics:
Along with the increase in orders comes the increase in returns. Therefore, companies must be prepared for the chaos that can be generated by the wave of returns and their proper management. Reverse logistics means higher costs in the warehouse: both in terms of personnel and space. Efficiency is becoming increasingly important so that logistics does not take up the entire margin. Picking processes are the key point in all logistics. If this simple operation is handled incorrectly, all the investment in the warehouse (building, shelving, forklifts, etc.) will have been for nothing, nor will all the expenditure on stockpiling.
Are you ready to succeed this Black Friday?
Omni-channel is more important than ever: 2020 marked a milestone in the rise of e-commerce in the wake of the Covid-generated health crisis. This milestone has also had an impact on Black Friday shopping, as consumers have new shopping habits.
To cope with the growth in activity, without making mistakes and minimising the costs involved in the internal logistics of companies, it is important to have the ability to adapt to these waves and be agile.
These are the solutions that we recommend:
BATCH PICKING
The workers in the warehouse have a single, optimised route, resulting in considerable time savings. The entire lot (more than 1 order) will be collected in a single journey, avoiding repetitions of the same route.
PICK TO LIGHT
The Pick To Light solution is a convenient, fast and intuitive system, which facilitate paperless order picking, keeping hands free.
PUT TO WALL
Workstations with individual spaces for each order. After the Batch Picking is complete, all the units must be sorted by order. The Put To Wall solution facilitates this process, thanks to Pick To Light Devices.
Take a look at our solutions, and contact us if you want to arrange a meeting.
Преимущества
- Наши решения разработаны для быстрой комплектации заказов и предотвращения ошибок обслуживания.
- Внедрение системы Рick to Light приводит к росту производительности и встречает превосходный прием у пользователей.
- Интеграция наших систем с пользовательскими информационными системами (SGA или ERP) проста и не требует много времени.